Greater Emphasis on Quality
Navigating the High Stakes and Complexities of Food Manufacturing
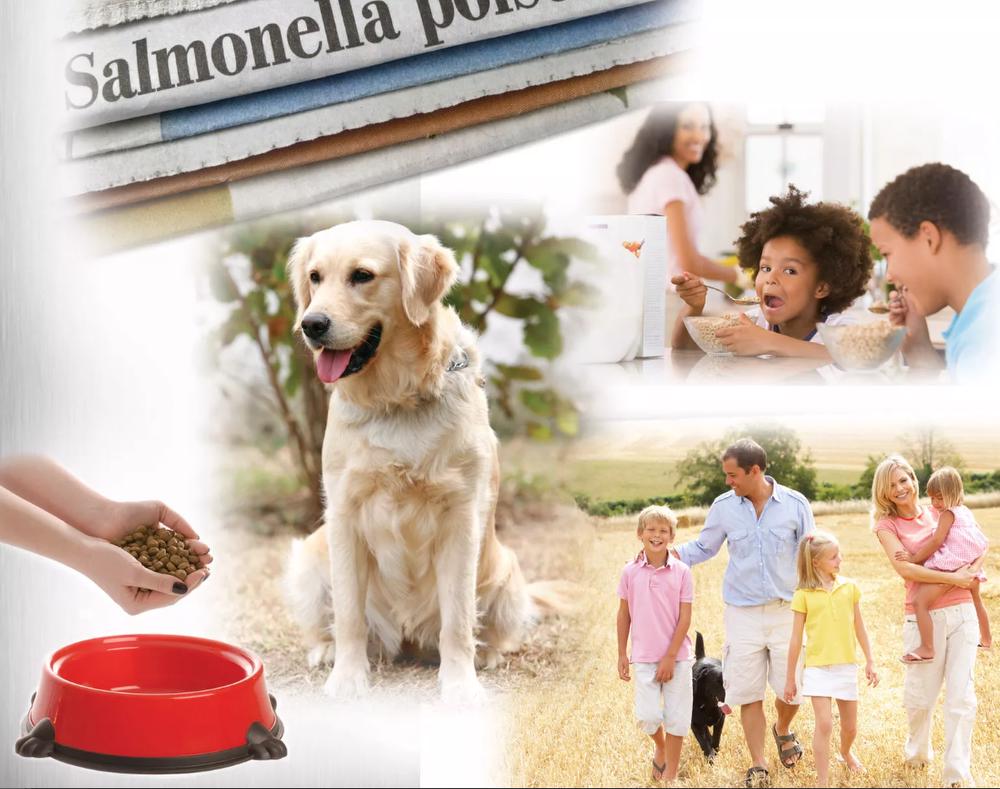
By Jason Lang, Vice President
Ask anyone involved in food production to name the greatest challenge facing the industry today, and food safety is sure to top the list.
Wave after wave of pet food recalls dating back to 2007 sent manufacturers scrambling to reassure regulators and the public they were operating safe production facilities. The widespread alarm forced plant closures, sent consumers into panic, and triggered rigorous standards for what previously had been rather loosely regulated processes.
The resulting new regulations, namely those part of the Food and Drug Administration Food Safety Modernization Act, brought much needed production improvements to the pet food industry, pushing them more closely in line with safety standards in human food production. But, these regulations also brought complexities that get more challenging to navigate every year.
The food safety crises of the past 10-12 years occurred in a time when the humanization of pets is very prevalent—pet owners are passionate and vigilant about what they feed their pets and have a growing interest in quality ingredients and formulations. Not only is food safety important to them, they want their pets to eat as well as or better than their families.
Quality is just as important on the commercial side. In the aquafeed industry, where confinement areas are especially susceptible to disease, producers need a more specialized formulation of feed that can protect against those diseases.
Quantity Matters, Too
The pet food industry is facing serious headwinds in areas tied to safety and quality, but another challenge felt among all facets of food production is the shared responsibility to feed a global population that’s expected to top 9 billion by 2050.
When you consider the fact that 68% of American households own a pet, humans aren’t the only factor in this global food conundrum—more people means there will be more animals to feed, so producing enough food to meet the demands of a growing population is a challenge facing those of us working in any capacity related to food, for humans and animals alike.
Addressing the Needs
As we wrestle with the enormous challenges before us, the question is what innovations will allow us to achieve our goals as an industry, and what sources will we utilize?
Extrusion technology is part of the answer. In fact, with the high heat involved in the cooking process, extrusion was one of the first processes to be recognized as food safe—and it undoubtedly will be a critical component in the future of food production. Extrusion is one method for making non-traditional ingredients look more palatable. For instance, take ingredients that are high in nutritional value but not seen as savory sources of protein—like insects and mealworms. These “edible insects” may be unappetizing to most people, but they could be important sources of protein for developing countries. They are cheap to produce, and through the extrusion process they can be ground and formed into something recognizable as food.
Finding an Expert to Lean On
Innovation has given us the means to create food that is safe from contamination and high in quality and nutritional value. This appeals to pet owners, who value healthy options for feeding their pets; and, it creates tremendous opportunities for food manufacturers.
But … recipes with nutrients and specialized formulations to help animals thrive are more complicated to produce and entail more specialized processing equipment. Those advancements come with more complex processes and sophisticated factory designs, all which can be daunting when you’re the one leading the charge.
Whether your extrusion-based project is for pet food, aquafeed, or human food, the stakes are high. If you’re setting up a new plant or making changes to bring an existing factory into compliance, now, more than ever, food manufacturers need a partner with the experience and expertise to help navigate a rapidly evolving and complex industry.
We will talk in an upcoming article about the areas where an outside partner can be invaluable to a manufacturing company trying to navigate the complexities of today’s food production environment. In the meantime, if you have challenges you’d like to discuss with an outside expert, please reach out to our team and we’d be glad to help.
Corporate Project Services, a division of Wenger Manufacturing, is a dynamic group of planning specialists backed by Wenger’s more than 80 years of process system supply to the industry. Our knowledge base and breadth of experience in extrusion processing and facilities construction is unsurpassed – and our commitment to excellence is recognized around the world.
More Articles
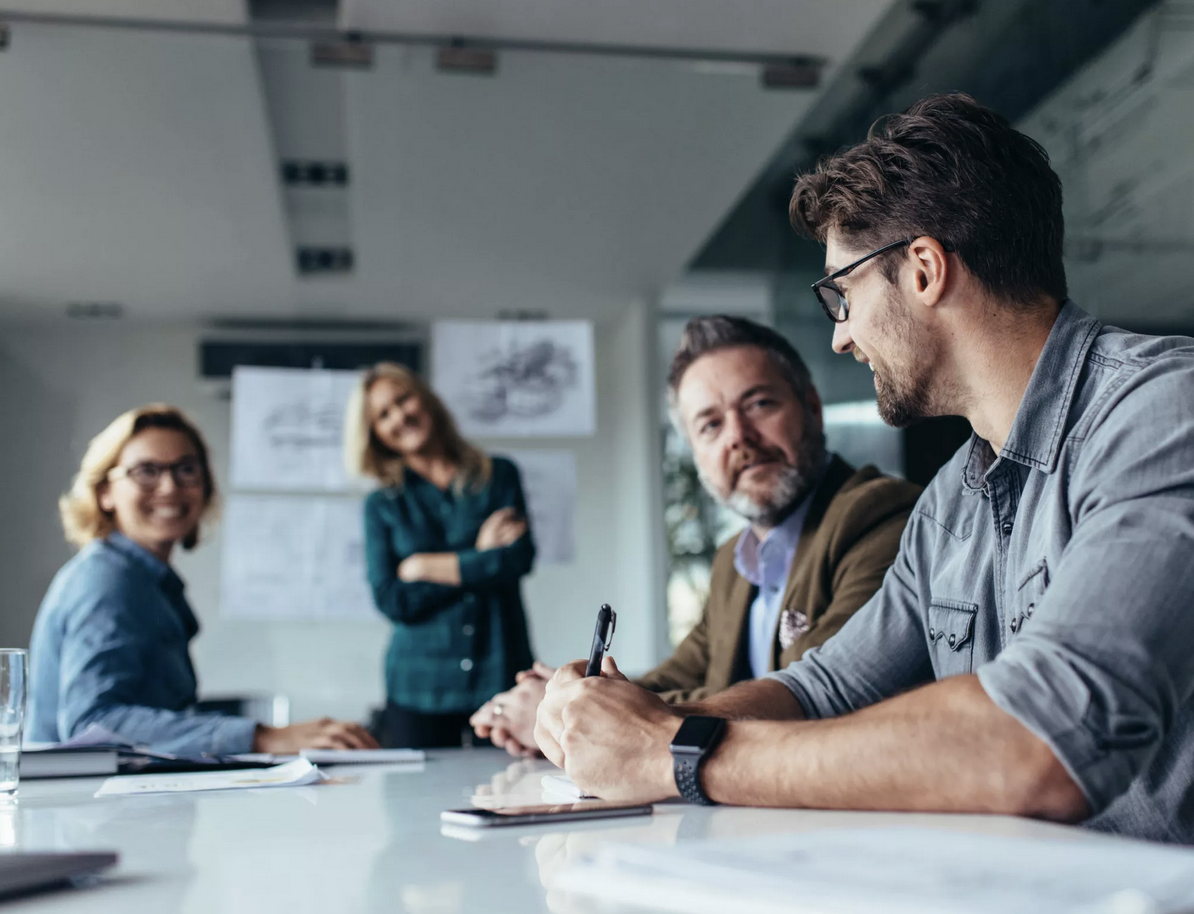
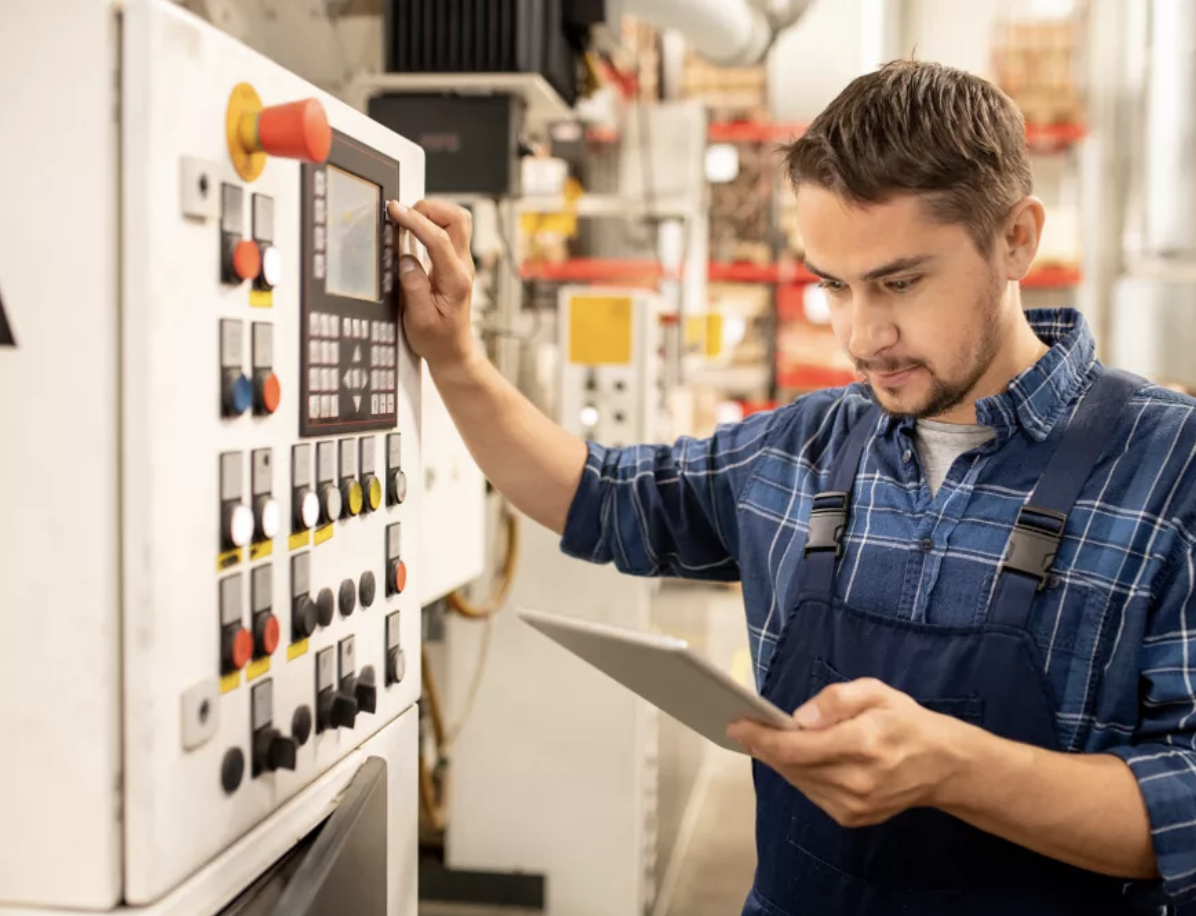
