The Changing Landscape of Extruded Food Manufacturing
“Better” Doesn’t Have to be “New” — Making the Right Choice for Your Food Extrusion Site
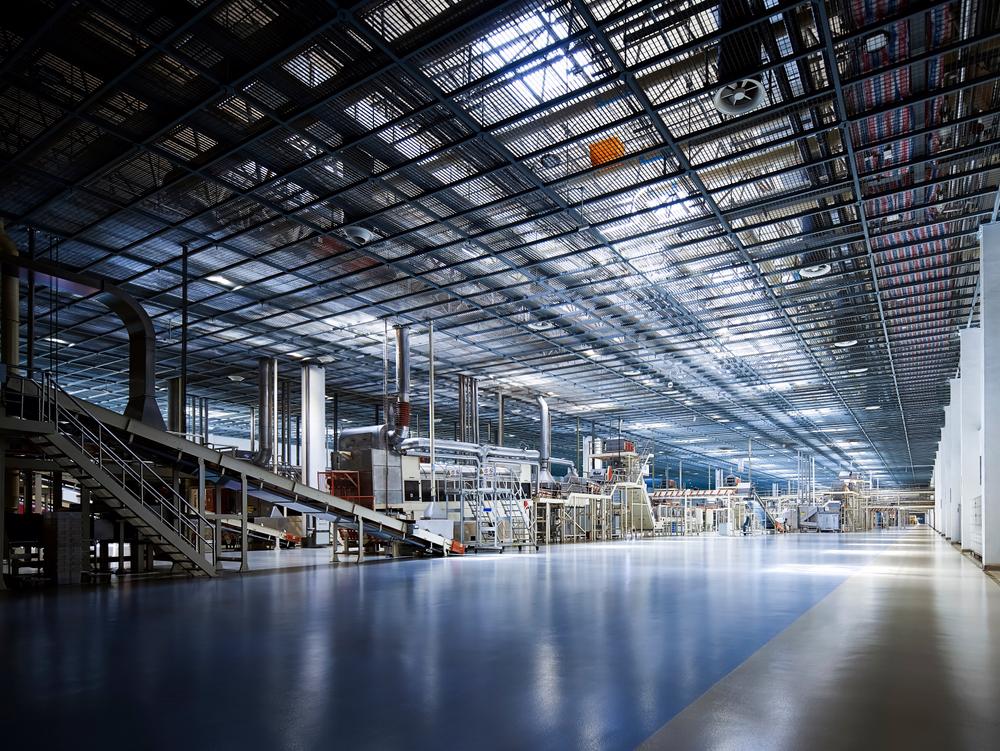
By Shaun Kibbe, Project Manager
Within the ever-evolving global economy, food production industries are continually challenged to adapt and reconfigure to meet the constant change in food demands. The extruded food sector is no exception. The reality for extrusion industries is they have high overhead costs of specialized production equipment, which elevates the financial liability of not responding in a timely manner to market trends and demands.
In a more robust economy, the traditional response to growing demand is to acquire new production equipment and expand production facilities accordingly. But, given today’s market dynamics, manufacturers are reevaluating their strategies and trending towards optimizing existing resources and enhancing their current production capabilities and available spaces.
The economic downturn has prompted extruded food manufacturers to reassess their capital investment decisions. Instead of dedicating resources into new facility construction, industries are strategically focusing on upgrades and refurbishment of current production equipment and maximizing the use of available or under-utilized existing spaces. This shift in focus is driven by the need for cost effective, fast and flexible responses to changes in market trends.
Upgrading Existing Equipment
Making upgrades to older or outdated equipment is proving to be a strategic move for many producers. Wenger, a pioneer in the extrusion industry, recognizes the importance of modernizing production lines to enhance efficiency, product quality and to bring older equipment and processes up to current safety standards. By investing in updated equipment components – or simply bringing the older equipment up to original specifications with investment in original equipment replacement parts – manufacturers can achieve higher and more consistent yields. This also allows them to reduce operational costs associated with waste reduction and higher yield percentages. Many upgrades bring outdated equipment into safety compliance with enhanced sanitary operation or by adding critical control points to enable automation or monitoring of food production.
Utilizing Available Space for Extrusion Capacity Expansion
Maximizing available space is another way many manufacturers are responding to economic challenges. Rather than bearing the cost of building new facilities, some manufacturers are focusing on optimizing production layouts and moving into underutilized brownfield areas for capacity expansion or product diversity. This approach not only minimizes the need for significant capital investment, it also provides some opportunity for streamlining production processes while maintaining proximity to existing upstream and downstream equipment and infrastructure.
Wenger’s Corporate Project Services
In this era of strategic upgrades and push for more efficient space utilization, Wenger’s Corporate Project Services (CPS) is a valuable resource for extrusion-based manufacturers. In fact, helping clients extract more value from their existing facilities is one of the areas in which we excel. Leveraging decades of expertise in the industry, CPS provides comprehensive solutions tailored to the specific needs of each client. We offer everything from facility configuration, process equipment selection, and sizing and layout, to project management.
Benefits of the CPS Process
- Customized Solutions: CPS understands one size does not fit all. Every project is customized to the client’s unique requirements, ensuring the solutions provided are aligned with the goals and specific constraints of each production site.
- Food Safety and Efficiency: A primary goal of every food manufacturer is achieving clean, ergonomic product flows, and upgrading existing equipment and utilizing available spaces with extrusion-centric layouts is often the smartest approach. This service allows manufacturers to achieve new product offerings with reduced waste and higher levels of food safety.
- Expert Project Guidance in Brownfield Sites: Upgrading existing, underutilized areas for capacity expansion – while often more cost-effective than starting over with a new build – is still an involved endeavor. Our CPS team of experts guides clients through qualifying a site then determining the appropriate configuration of the available space. Our 3D scanning technology allows us to model available space and provide 3D drawings to help clients visualize an updated production line.
Economic pressure coupled with higher interest rates has necessitated a strategic mindset shift for food manufacturers. Wenger’s Corporate Project Services plays a pivotal role in guiding clients through this challenging period by offering tailored solutions that align with the extrusion industry’s evolving requirements. If you prioritize upgrading current production lines and transforming underutilized spaces into food production zones, CPS stands as a reliable partner. Together we can seamlessly integrate these upgrades to improve your product offerings with increased efficiency and food safety.
If you want help transforming your space for more throughput or efficiency, please reach out to our team.
Corporate Project Services, a division of Wenger Manufacturing, is a dynamic group of planning specialists backed by Wenger’s nearly 90 years of process system supply to the industry. Our knowledge base and breadth of experience in extrusion processing and facilities construction is unsurpassed – and our commitment to excellence is recognized around the world.
More Articles
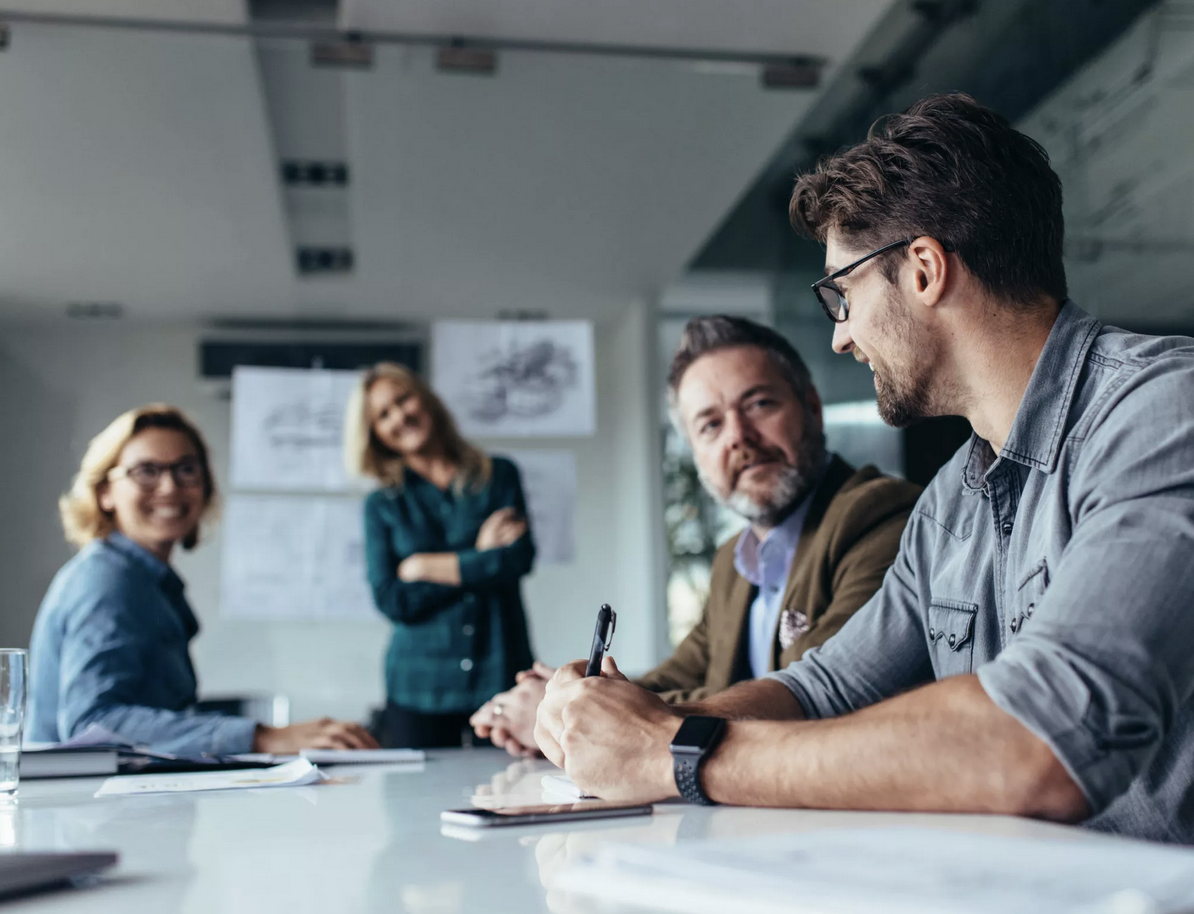
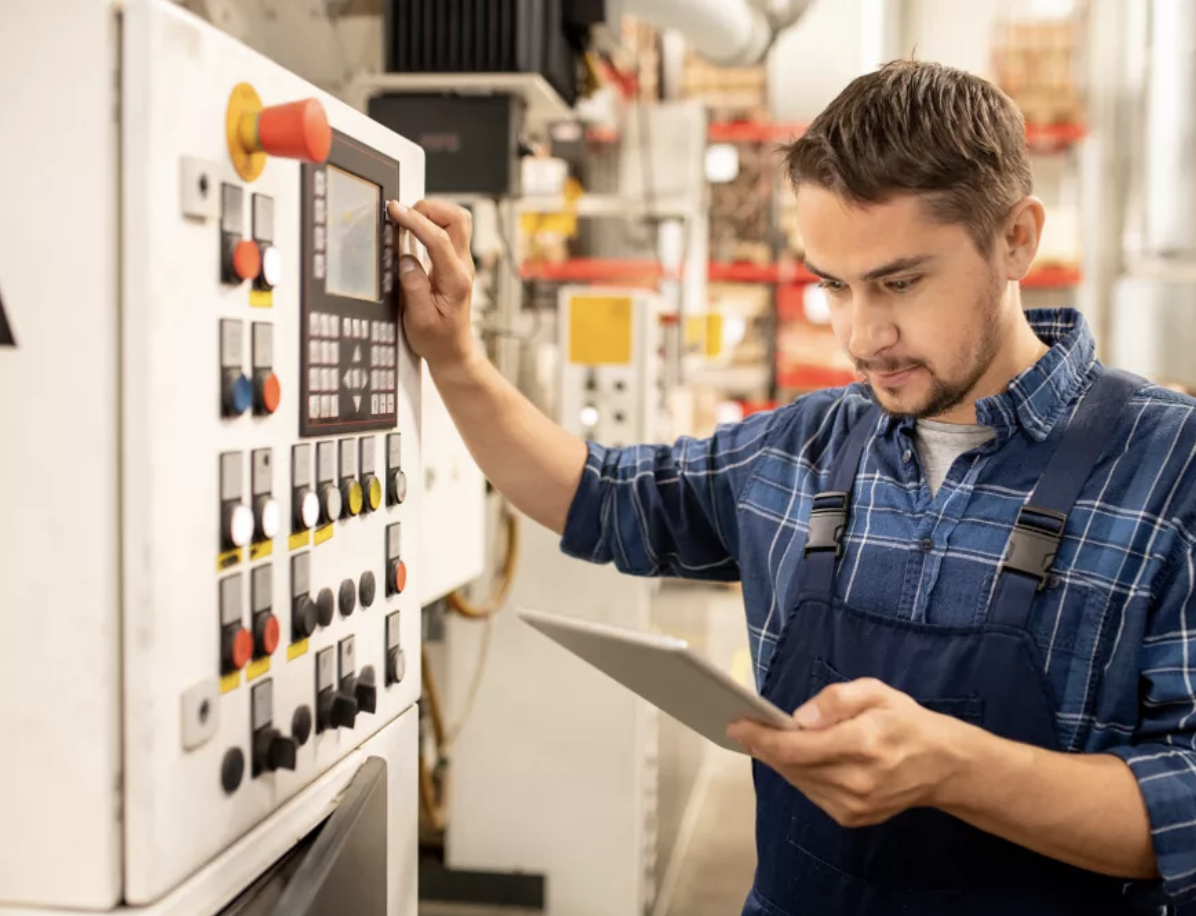
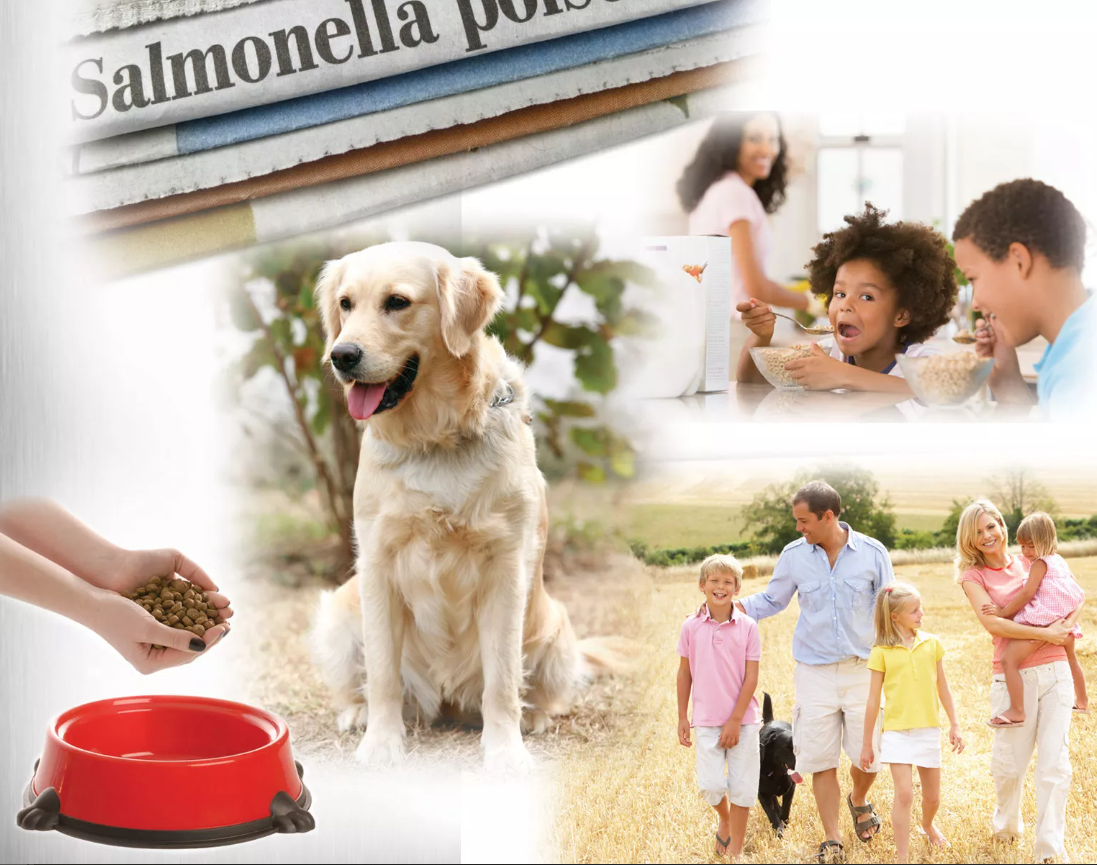